Interviewee: Dr. Giovanni Dorin, Marketing and Business Development at Officine Mario Dorin
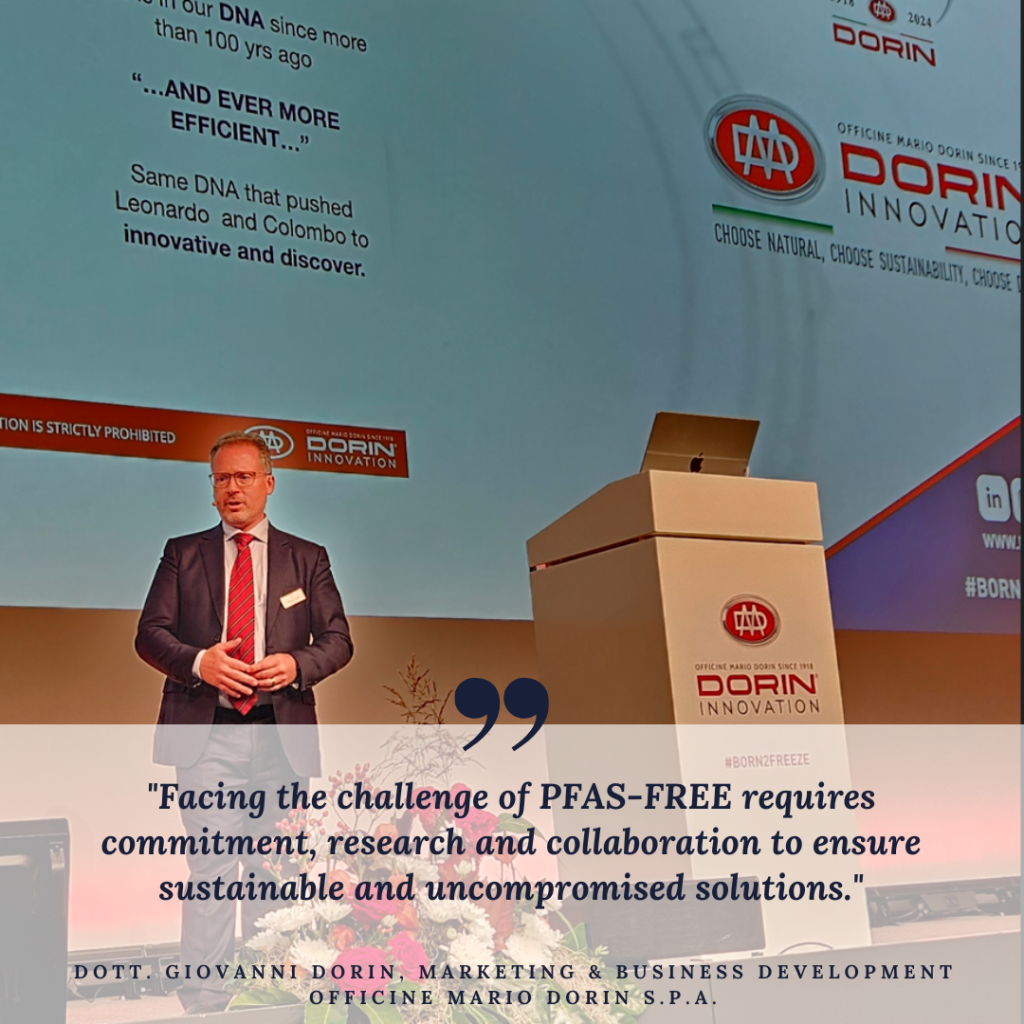
What is the current use of PFAS in refrigeration compressors? What technical advantages do they offer? Are they essential and why?
Currently, PFAS are present in various compressors components, both directly (in the materials used) and indirectly (in manufacturing processes). These materials have essential characteristics such as chemical resistance, thermal stability and low friction, which are crucial for ensuring reliability, safety and efficiency of compressors.
The use of fluoropolymers, such as PTFE, plays a key role in reducing friction, improving energy efficiency, and ensuring long-term reliability. Eliminating them without suitable alternatives could significantly compromise the performance and safety of RACHP systems.
How do you assess the impact of a potential ban on PFAS use?
A total ban on PFAS would have a significant impact on compressor production and their key characteristics. The main challenges involve both the materials used and the manufacturing processes during product assembly, as well as certain refrigerant gases employed afterward. Moreover, replacing fluoropolymer-based materials could lead to reliability issues, reduced lifespan and lower energy efficiency in compressors. The entire industry is awaiting clear guidelines and fully qualified, validated alternatives to plan potential transition in a sustainable manner.
Are there any alternative solutions to PFAS in sight or already used?
Officine Mario Dorin has long been conducting a mapping process with its suppliers to identify PFAS-free materials and evaluate solutions that comply with quality and safety standards. At the same time, we collaborate with ASERCOM to understand the applicability of regulations and research alternative materials that can ensure the same operational efficiency without compromising system sustainability. Additionally, we are also participating in a European program, “PFAS FREE COOLING & HEATING”, which is committed to the use of natural refrigerants and PFAS-free technologies to protect both the environment and public health.
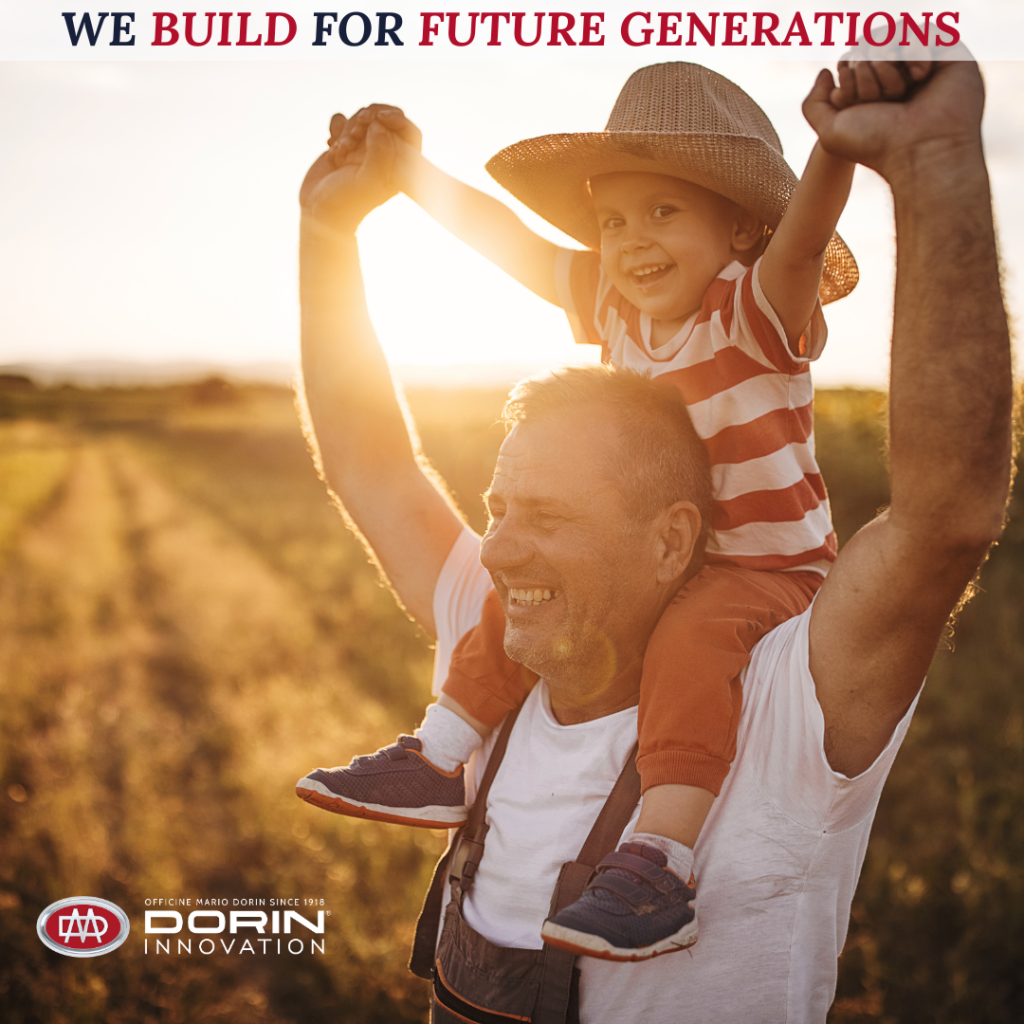
What technical changes do you consider necessary to adapt to a PFAS-free future?
From an engineering standpoint, replacing PFAS would require an in-depth review of materials and processes. For example, components that currently do not have validated and available alternatives include bearing bushes, motor winding cable insulation, electrical components and certain seals.
These components would need to be redesigned with alternative materials that guarantee the same performance. However, the process of validating new solutions takes time.
The RACHP industry is also facing new challenges, both due to the use of natural refrigerants with characteristics that are sometimes different from those used until now (flammability, high pressures and operating temperatures), and due to new applications such as high-temperature heat pumps, which bring additional challenges for the compressor and some of its components.
Moreover, the phases of decommissioning PFAS-containing components require a disposal to be carried out professionally to minimize environmental impact. We believe that a complete transition could take several years, depending on the availability of qualified, validated and reliable alternatives.
Is there anything I haven’t asked that you think is important to highlight?
The refrigeration industry has already faced complex transitions toward more sustainable solutions in the past. A concrete example is the adoption of CO₂ as a natural refrigerant, a path where Dorin has been a pioneer since 1991, anticipating industry trends by decades and developing this technology well before our competitors. Similarly, the transition to PFAS-free materials must be approached with a structured strategy, based on research and development, to ensure that the performance and reliability of systems are not compromised.
Dorin is already engaged in the development of innovative technologies, such as high-temperature heat pumps, which represent a new frontier for the refrigeration industry.
These challenges don’t scare us, they are part of the environment in which a company like ours has always operated and they are in our DNA since the time of our founder, over 107 years ago. Facing them means finding reliable, efficient and safe solutions, and for these reasons we believe collaboration with other companies in the industry is essential. This is not an individual effort, but the result of a collective effort. Because we care about the health, future and sustainability not only of our sector but also of future generations, we actively collaborate with ASERCOM and the European program “PFAS FREE COOLING & HEATING” to ensure a structured and shared approach. We do not proceed haphazardly, but through a continuous exchange of information and know-how, with the aim of identifying viable solutions as quickly as possible.
We believe that a balanced and coordinated approach between the manufacturing sector and legislative institutions is essential to achieve environmental sustainability that is truly sustainable for the industry. This allows us to continue offering products that ensure high performance, reliability and efficiency, as well as public health safety, while considering both environmental sustainability and the need to guarantee high performance in RACHP systems. We remain committed to researching alternative solutions and engaging in dialogue with institutions for an effective and sustainable transition.