
By 2050, the European Union wants to be “clean”, meaning with zero net carbon emissions. If it succeeds, it would be the first “continent” to achieve the carbon neutrality.
To hit this target, the Union is committed to speeding up the decarbonization of its economy and to promoting an ambitious diffusion of renewable energy sources. For industry, this means achieving energy efficiency and electrifying those processes that until now have used fossil sources for their management. Nowadays, one of the industrial processes mostly depending on fossil sources, but with broad electrification possibilities, is the production of process heat, an ambit that is little talked about but where there are not only noteworthy potentials of energy efficiency improvement but also interesting development opportunities for the refrigeration industry.
Energy use in the industrial sector
The process heat is quite ubiquitous and is used for the production of industrial goods – such as chemical products, steel, paper, glass, foods and drinks – but also to carry out real manufacturing phases – sterilization, drying, food treatments and so on. Today the process heat constitutes the single most significant energy use for industry but numbers indicate that in a frame of energy transition it is not secondary indeed. Currently, the process heat is
the largest energy use in the industrial sector: it represents 47% of the demand for industrial energy and it is responsible for about three fourths of the CO2 emissions generated by industry. The energy for the process heat is preponderantly supplied by natural gas (35%), carbon (27%) and other fossil fuels, whereas the electricity (4%) and the biomass (5%) are the energy sources least used. On the whole, fuels of fossil origin represent about the three fourths of the energy consumed for the process heating.
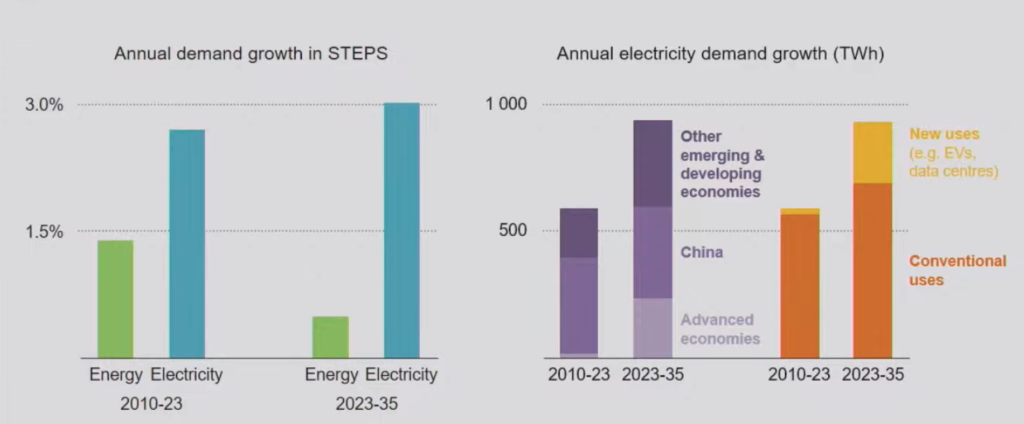
Electrifying is possible
However, according to a recent report by the renowned institute Fraunhofer ISI[1], already today there is a broad range of electrification technologies that can satisfy specific process requirements. Heat pumps and electric boilers, for instance, can respectively generate up to 200 and 500 Celsius degrees for chemical processes. Electric arc furnaces are widely used for the production of steel at 1,800 degrees. Technologies such as the resistance heating, the induction heating and electric steam crackers will be available in the course of next years and they will cover all intervals, from 100 to 2500 degrees. Direct electrification technologies, which are expected to be available within 2035, could satisfy 90% of the demand by the European industry for not electrified energy, yet. At present, the available technologies can already supply over 60% of this demand.
Industrial heat pumps, interprets of the industrial electrification
As mentioned in the previous paragraph, among the useful technologies for the decarbonization and the electrification of industrial processes, there are undoubtedly industrial heat pumps, with thermal powers exceeding 200 kW. They are from three to five times more efficient at low and medium temperatures in comparison with conventional systems and they could supply over 10% of the demand for industrial heating and for district-heating under 200°C within 2030.
Although it is not a new technology, the technological highlight of industrial heat pumps is starting being acknowledged to a wider extent just nowadays. According to a study by McKinsey[2], recent trends, such as the boost to decarbonization and to the heat electrification, economic factors and the Governments’ support through regulations and incentives mean the industrial heat pump market is set to rise dramatically, with a forecast growth by over 15% yearly until 2030.
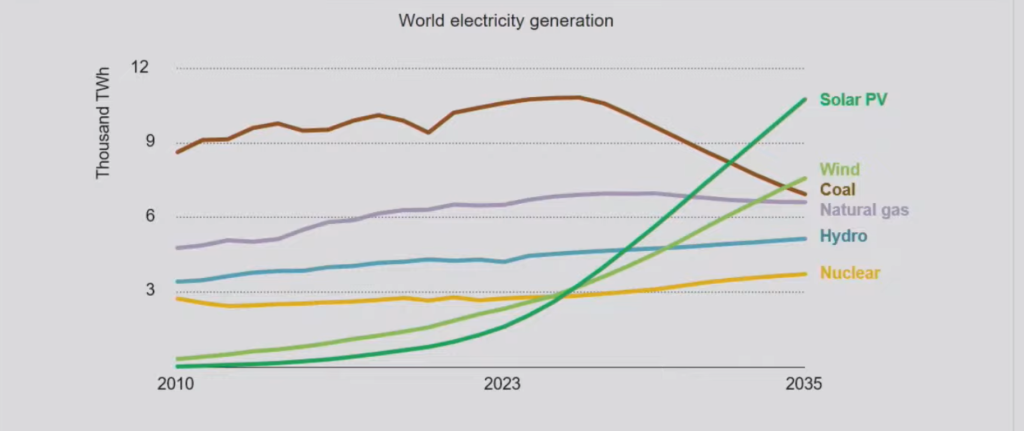
Recovery, not only manufacturing
The European Heat Pumps Association (EHPA) has recently published a document entitled “Waste into Wealth: How Heat Pumps Can Recycle Heat to Save Energy – and the EU Policy that Matters”. The document underlines the significant potential for the waste heat recovery with heat pumps to improve the energy efficiency, to decrease emissions and to contribute in the EU targets of net zero.
The document underlines the value of the waste heat, which can satisfy a substantial part of the European requirements of buildings, industrial processes and hot water. Capturing the waste heat and bringing it to higher temperatures, heat pumps can deliver efficient heating and cooling, replacing fossil fuels and decreasing the consumption of primary energy. According to EHPA, the recovery of waste heat has the potential of letting the EU save about 67.4 billion Euros yearly by 2050, corresponding to Slovenia’s GDP. Such recovery would also relieve the pressures on the electric grid, offering a sustainable energy solution for residential and industrial applications.
Heat pumps can capture and reuse the waste heat, bringing it to a significantly higher temperature. The recovery of the waste heat with heat pumps needs three components:
- A waste heat source
- A thermal energy network to store and distribute heat
- A user that needs energy.
Heat sources may be industrial processes, data centres, commercial offices and buildings. The waste heat is often the result of cooling processes. Heat networks, also known as district heating and district colling, can operate at environmental temperature or, if insulated, at higher temperatures. Heat users may be commercial or public service (hospitals, offices) buildings, industrial processes or district heating networks at high temperature. The combination of heating and cooling applications can create synergies among different end-users, for instance by connecting data centres to district heating networks. In these systems, heat pumps can cool data centres and recycle the waste heat in district heating networks. In this case, the heat pump usefully uses the thermal energy for both systems. The use of heat pumps contributes in improving the energy efficiency in various applications and reduces the need of generating “new” energy.
Creating an ecosystem of users
The efficiency of heat pumps can be increased by connecting buildings with complementary heating and cooling requirements, allowing, for instance, the heat coming from the cooling system of a building to be reused for the heating of another. Let us take the case of data centres: they consume high quantities of electricity to process information and therefore they produce large quantities of waste heat. According to IEA – International Energy Agency, in 2022 data centres’ global electricity consumption was 240-340 TWh, amounting to around 1-1.3% of the global electricity demand. With 17,000 networks of district heating and district cooling that supply 67 million Europeans in the whole continent, the recovery of waste heat is a consolidated solution in urban areas.
Advantages of electrification
Electrifying industry is not only necessary to reach decarbonization goals; not only possible because technologies exist or will exist in the short term but, under various respects, desirable, too. Among the advantages that would derive to industry from a process electrification, it is worth mentioning:
• A noteworthy reduction of emissions
• More energy independence
• A higher efficiency because electrical processes are more efficient than those based on fossil fuels (let us just think of an electric motor versus an internal combustion engine)
• The possibility of an integration with a (self)-production of renewable energy and of an easier process integration with the digitalization;
• More industrial competitiveness, especially versus foreign competitors like China, Asia and United States
Strictly speaking, however, we must recognize that, despite the advantages and the broad possibilities, objectively there are still some difficulties. For instance:
• the high costs, especially connected with electricity costs, which are higher than gas ones;
• the need of more appropriate infrastructures, mainly concerning electric grids to support a demand increase
• the resistance to change by consolidated industrial sectors that may be reluctant to shift to new technologies.
The electrification era
Actually, the world is moving towards the electrification. At the end of 2024, IEA – International Energy Agency – presented its report World Energy Outlook 2024. Fatih Birol, Director of the Agency, affirmed: «In the past, there was a carbon era, followed by an oil era and now we are clearly entering a new era, the electricity era». The world goes towards the electrification, not only for the final uses of energy but also for the production. In 2024, over 80% of the new generation plants built in the world were for renewable energies.
On the demand side, the demand for electricity grows more quickly than the general energy demand and in 2035 – according to IEA projections- the wind and photovoltaic generation will exceed the one from gas and carbon. Demand drivers are not only new applications like, for instance, the mobility electrification but also more “traditional” applications such as data centres and conditioning. «Let us just think – Birol states – that in Japan and USA 90% of houses are equipped with air conditioning but in Nigeria only 5%, in India 20%, in Indonesia 15. With a changing climate, anyway, these numbers are clearly expected to rise».
What does more electrification mean for the cold industry?
Undoubtedly, the transformation towards an increasingly electrified economy implies enormous changes of industrial, economic and geopolitical nature. As the World Energy Outlook highlights, although with different rates, these changes are taking place all over the world and they will become more and more pronounced as the Planet progresses in its decarbonization efforts.
There are some basic considerations that industry – also the refrigeration one – must make in this context of market change:
- We need new competences: industry must invest in research and development to design more efficient systems consistently with the sources of electric renewable energy;
- The electrification of appliances and of processes implies the adoption of advanced and new technologies. The system electrification, for instance, could favour new forms of electrification forms that have so far remained in the shadows, like the magnetic refrigeration;
- The increase of the demand for “smart” refrigeration systems that require advanced control and automation skills.
- The increase of the demand for advanced electrical components such as high-efficiency motors, smart sensors and energy storage systems;
- The adaptation to the business model:
- Increase of after-sale services, such as remote maintenance and software updates;
- Subscription models for the use of forefront technologies (ex. Connected systems);
- Integration of energy solutions: manufacturers could collaborate with renewable energy suppliers to offer complete packages (for instance, refrigeration plants powered by photovoltaic).
- Resilience and Integration with the Smart Grid: electrical refrigeration systems can be integrated with smart grids to manage energy consumptions dynamically;
- Let us consider the energy storage: the electrification allows the use of batteries to power refrigeration systems during consumption peaks or in absence of electric grid.
[1] Fraunhofer ISI (2024): Direct electrification of industrial process heat. An assessment of technologies potentials and future prospects for the EU. Study on behalf of Agora Industry
[2] “Industrial heat pumps: five considerations of future growth” McKinsey&Company, 2024